Craig,
The generator test setup's three phase motor could do with more oomph, but you make do with what you can scrounge from work . . .
The other problem's got to do with switching transients in the dummy load. I'm using low-dropout voltage regulators with booster transistors as constant-current loads. All fine in theory, but the practice is a different matter. The regulators can turn off way faster than the generator can react. I had an FJ Bosch generator on full song, and turned the 20A load off. There was a coughing sound, and the magic smoke came out. The field current had to decay somehow, and it did so by generating a huge voltage spike, which took out the lower-current sections of the dummy load, and the cooling fan.
I've thought up a soft-start and -stop system, but it'll use a voltage reference and op-amp instead. Still to be implemented.
And don't admit that you've had experience at rewinding DC machine armatures. I have a couple of 6V Delco generators needing armature rewinds . . .
Rob
Hi Rob
Had a think about setting up a test rig similar to what is shown in the manual. The setup in the manual has a few features that aren't required to do the testing required if set up to test generator/regulators on and off the vehicle and may be a simple solution to the smoke issue. Given the smarts out there a fan could be added cheaply that can handle 6-24V so the test rig itself could be used on old style 6-24V generator/regulator setups. This is the solution I have in mind:
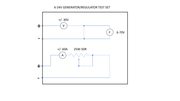
Interested if you think this soulution would overcome the problem - something I intend to knock up for the shed so I can test. I will build a prototype and test it out then see what I can fabricate in an old style wooden boz with a bit of stainless for character.
For driving the bench test setup I am in the same boat and have a couple of three phase motors sitting around. Definitely need a viable speed drive to simulate RPM variations for bench testing. I will try lay my hands on a single phase motor as the ones I have are quite heavy. I use a capacitar start system to get them running on single phase and a drive to regulate the RPM.
As for rewinding armatures; it is either winding by hand, which is tedious or potentially adapting a manual coil winding machine by adding an arm to guide the wire around the armature slug to spin (and count) the winding number. I think the key to this is being able to hold the armature vertically and secure it while it is being wound. A jig for the field windings could be made for a few scraps of timber but a tow piece aluminium casting would be sweet as it would be very easy to get the windings off the jig. Once the jig(s) is/are built it then becomes finding a source of new commutators, wire and finding some time to do the work.
have a heap old pistons that are dying to be melted down into something useful; and I expect I now have a plan for them. I just need to retire so I can get cracking on it; only a few more years! In the meantime I will find a couple of dead gennys to "experiment" on.
Cheers n Beers
Jolls