So how do we balance this up? Modelling a pushrod that is being bent in compression is not an easy thing. Equally, we don’t need answers to seven decimal places. The easiest way to model a bending pushrod (and accurate enough for what we are doing) is to treat the pushrod like a simple beam being bent:
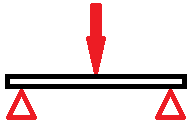
Assuming a pushrod with outside diameter D, and for the hollow ones with an inside diameter d,
a) The bending load on the solid pushrod is inversely proportional to the diameter
4. For the hollow pushrod, it is inversely proportional to (the difference in inner/outer diameter)
4.
i.e. stress α 1/D
4 for the bar, and stress α1/(D
4-d
4) for the pipe.
b) Weight is proportional to the diameter
2 for the solid pushrod, and proportional to (the difference in inner/outer diameter)
2 for the hollow one.
i.e. weight α D
2 for the bar, and weight α(D
2-d
2) for the pipe.
As examples, taking a solid 3/8” pushrod and increasing the diameter to 7/16” will halve the bending stress in the pushrod, but increase weight by a third. Replacing the same 3/8” pushrod with a 7/16” hollow pushrod with 0.080” wall thickness will reduce the stress by 40% (less than the 50% of the solid 7/16” ones), but will reduce weight by 20% (compared to the 33% increase in weight of the solid 7/16” ones).
One trick that the racing fraternity has been using for some time is to cut the ends off old hollow pushrods, and insert a thinner tube into the two old ends. This was recently done by Ellis, using some 0.035” walled chrome moly tubing. Looking at Ellis’ new pushrods:
a) original solid pushrods are 0.252” outside diameter
b) replacement pushrods are 0.372” outside diameter and 0.035” wall thickness (0.302” internal diameter).
Ellis’ pushrods have only one third of the bending stress than the original GMH pushrods, and will be some ¾ of the weight.
An alternative would be to take the standard GMH pushrods, cut the ends off and slip the ends into a larger chrome moly tube. The resultant pushrod strength (and weight) would depend on what tube wall thickness is used. As a guide for this scenario:
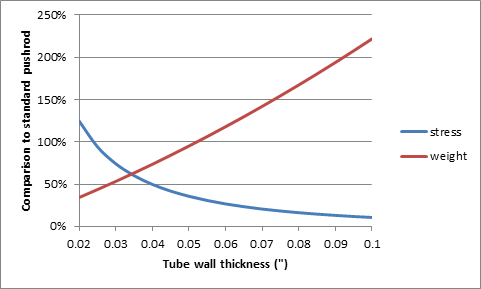
The graph above shows that tube wall thicknesses of 0.024” and thicker would have the same or less stress than the standard pushrod, whilst wall thicknesses of 0.052” or thinner would have the same or less weight than a standard pushrod. In short, if you want to take a standard grey motor pushrod, cut the ends off and insert them into hollow chrome moly steel tubes, the wall thickness “sweet spot” range is between 0.024-0.052”.
As a comparison, looking at some typical pushrod manufacturers:
• Manton make pushrods in 0.035-0.168” wall thickness (3/8”-7/16” outside diameter),
• Trend make 0.080-0.188” (5/16”-3/16” outside diameter), whilst
• TrickFlow make 0.080”-0.135” wall thickness (5/16”-3/8” OD).
Cheers,
Harv