Harv
|
 |
« Reply #260 on: November 01, 2014, 03:36:56 PM » |
0
|
With the manifold all prettied up, it’s time to think a bit harder about our relief valve. I’ve used the aluminium plate type valve favoured by Eldred, which consists of two aluminum plates (one circular, one triangular). Dimensions for the plates are shown below. 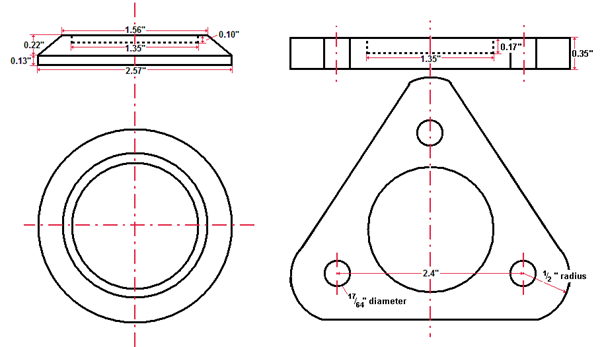 Note that at the dimensions shown, the three ¼”UNF mounting bolts/studs do not quite clear the circular disc – either make three small notches in the disc, or increase the 2.4” measurement above slightly to space the bolts further out. A hole is cut into the top of the manifold using a holesaw to allow the gas to pass out through the relief valve. From earlier postings, we need a minimum of a 2¼” diameter hole for red motors, and no less than a 1 9/16” (a little over 1½") hole for grey motors. These dimensions will give a sealing face (a ring shape) of 5/32” and ½” thick respectively. The hole I cut in the manifold above is 1.73” (a poofteenth bigger than the 1.68” internal width of the box section, and hence as big as can be done with that manifold). Note that the valve need not be mounted on the top of the box section – it will work equally well on the side (though avoid the bottom of the box as it will tend to accumulate any dirt, oil or condensing fuel, making the valve unreliable). I used some rubber sheeting under the circular plate to act as a gasket. You could also use normal paper gasket, but bear in mind that what comes out the valve is flaming, ignited fuel/air at a great rate of knots. Paper may not survive, and a leaking relief valve will sideline you in the Woolies carpark. I also drilled three holes for the relief valve mounting bolts, and tapped them to suit ¼”-28UNF. I’ve used bolts here. The position of the relief valve bolts (how far they are screwed into the manifold) determines the spring compression, and hence the pressure setting of the valve. The more they are screwed in, the higher the valve set pressure. The only down-side of using bolts is that the bolt holes go all the way through the manifold (i.e. they are not blind). This means that gas can pass from the manifold up the threads, causing a leak. The bolts will need to be sealed (with thread sealer, just like some water jacket bolts on cylinder heads) when they are finally tested and set. It is probably neater to use studs, with nuts on the top to adjust. The studs can then be permanently sealed into the manifold. As a note, the bolts (or studs) used should be high-tensile, as they are under a pretty fair load constantly – mild steel may stretch over time.
|
|
|
Logged
|
|
|
|
Harv
|
 |
« Reply #261 on: November 01, 2014, 03:37:30 PM » |
0
|
The relief valve uses a (used) Holden grey motor valve spring to provide pressure. These have a spring tension of some 85lb/inch (i.e. if you compress the spring ½”, it exerts 42.5lb of force, if you compress it 1” it exerts 85lb of force). At 1” of compression we are very close to coil bind, meaning the maximum force we can exert with this spring (by compressing it 1”) is 85lb i.e. we can adjust the spring to deliver from 0 to 85lb of force on our aluminium disc. For the hole I cut (1.73” diameter), we have a cross sectional area of some 2.2inch2. By acting over the 2.2inch2 of manifold hole, the manifold pressure would need to rise to approximately (85lb ÷ 2.2inch2 =) 39psi before the spring is overcome and the valve lifts (at maximum spring compression). All up, it means we have an adjustable relief valve that can deliver from 0psi to 39psi. Cut the hole a little bigger, and you can handle a little less pressure. Use a stiffer spring, and you can handle more pressure. From previous posts, we set the valve at 150% of the targeted boost pressure. If we target 10psi boost (realistic for a Norman), we set the valve to 15psi. With the valve assembled, it is now time to undertake the pressure test. The intent of the pressure test is to check that relief valve pops at the right pressure… too low and we will leak fuel/air, and too high and the manifold may rupture. The idea here is to test at multiple spring compressions. Having done that, for a given spring we will know that say 0.5” of compression gives you say 3psi setting, 0.8” compression gives you 8psi etc. That way you will not need to pressure test the manifold again if you pull the valve apart, just adjust it to the right compression distance. I made some blanking plates out of galvanized plate for the three runners, and out of vinyl-coated chipboard for the supercharger hole. I have glued some rubber sheeting to the plates with contact adhesive to serve as gaskets during pressure testing. 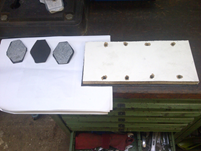
|
|
|
Logged
|
|
|
|
Harv
|
 |
« Reply #262 on: November 01, 2014, 03:38:21 PM » |
0
|
The blanking plates for the runners were held in position with clamps, whilst I used the supercharger mounting holes to clamp on the chipboard blank. You will need to plug off any spare tappings in the manifold with steel or brass plugs. To measure the pressure, I used the same boost gauge I intend to use in the vehicle. When pressure testing, it is important to check each time that the valve is adjusted square. I measured between the top and bottom plates (see photo), and adjusted the bolts to square up the valve. 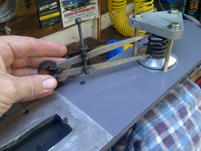 The “zero” setting (i.e. the valve only just seated, with bugger-all spring tension) is a measurement of 1.94”. I used some soapy water around the relief valve to detect the onset of leakage, and the air compressor (gently!) to bring the manifold up to pressure. Be wary here that if you are heavy handed, or the manifold is weak it can go bang and throw steel at high speed for a long distance - good idea to clear the shed and wear a faceshield for this one. Once you have finished the testing (and confirmed tha the vavle pops at the right setting), the valve must be locked. There is a risk that the bolts either vibrate loose over time (leading to leakage from the valve), or are accidently tightened right up in the future (leading to the valve not opening when it needs to). To prevent this, I have cross-drilled the bolt heads and fitted safety wire (I love drilling 1mm holes through high-tensile steel bolt heads on an angle). Safety wire works by connecting the bolts together in pairs. If one bolt tries to vibrate loose, the wire pulls on its partner. The wire is installed in such a way that the bolt being pulled on tries to tighten up. This provides resistance, and stops the first bolt from loosening. The wire also acts as a reminder that the nuts should not be played with (and hence inadvertently tightened). 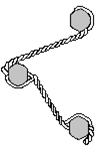 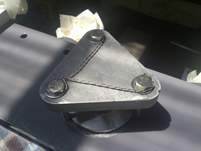 You could always use locknuts, Loctite or jam nuts… I think lockwire looks cooler though. Those forum members with an aviation background are cordially invited to stop laughing at the quality of my lockwiring… at least it’s better than my welding . I know that this seems to be a lot of stuffing around for the relief valve. Bear in mind that we are protecting the car (and anyone around it) from an uncontrolled explosion. Blower bangs are pretty common in race vehicles, though hi-powered dragsters are normally fitted with blower restraints (webbing) to hold the bits together during a bang. Our old Normans normally don’t use blower restraints. Anyone who is still not convinced that a supercharger bang is a major event should watch this video: https://www.youtube.com/watch?v=Ll3EvNMBgLA. Cheers, Harv (deputy apprentice Norman supercharger fiddler).
|
|
|
Logged
|
|
|
|
|
FCRB26
|
 |
« Reply #264 on: November 01, 2014, 05:41:38 PM » |
0
|
Thanks for the plug only just seen it ?
Did the blow off plates need modifying?
|
|
|
Logged
|
|
|
|
Harv
|
 |
« Reply #265 on: November 01, 2014, 05:45:33 PM » |
0
|
G'day Pete,
Nope, the blowoff plates were perfect for the grey motor valve spring. The only mod I needed to make was to make three tiny notches in the disc to clear the three mounting bolts/studs - could perhaps space out the holes in the triangular plate a poofteenth more, but no drama with the notches.
Cheers, Harv
|
|
|
Logged
|
|
|
|
Harv
|
 |
« Reply #266 on: November 01, 2014, 05:46:18 PM » |
0
|
Ladies and gents, In the post below, I am going to cover the way that the ignition system can be changed to reduce knocking (pinging) in our supercharged grey motor. By retarding the timing, the engine will have less tendency to knock. Our standard Holden grey motor has three separate components to ignition timing: a) Advance which is added by rotating the distributor then bolting it down. This is often referred to as “flywheel advance”, and is constant regardless of what the engine is doing. For a grey motor, this is typically 2º. b) Mechanical advance (sometimes called centrifugal advance). This is accomplished inside the distributor by a combination of spinning weights and springs, and varies with engine speed. It works by rotating the top of the distributor shaft clockwise to open the points earlier. For a grey motor, the following is a typical mechanical advance curve: 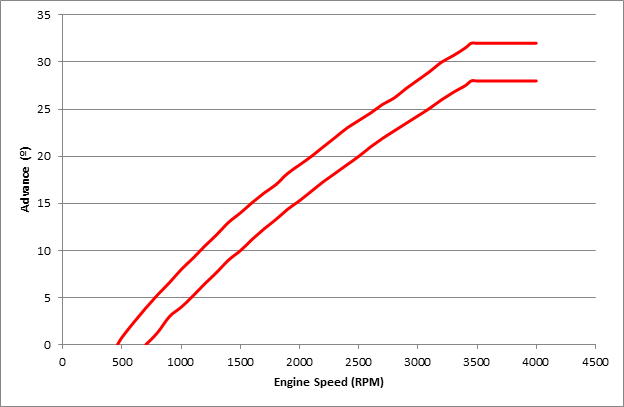 Note that there is a range of advance for a given engine speed (between the two red lines), as not all distributors are quite the same. The faster the engine spins, the more the distributor advances the timing (up to 28-32º at 3450rpm). The mechanical advance component can thus be described as “28-32º all-out at 3450rpm”. c) Vacuum advance. This is again accomplished inside the distributor, but is driven by the vacuum module sitting on the side of the dizzy. The module is connected to the inlet manifold – the more vacuum in the inlet manifold, the more the vacuum module advances the timing. It works by rotating the breaker plate (and the points attached to them) anti-clockwise to open the points earlier. For a grey motor, the following is a typical vacuum advance curve: 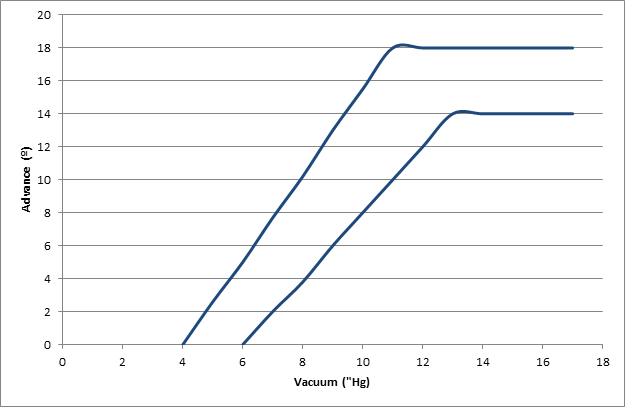 Note that there is again range of advance for a given vacuum (between the two blue lines), as not all distributors are quite the same. The higher the engine vacuum, the more the distributor advances the timing (up to 14-18º at 10-12”Hg of vacuum). The total timing advance we get is thus a combination of flywheel advance (how far the dizzy body is turned), mechanical advance (how far the dizzy shaft top is turned) and vacuum advance (how far the points are turned), and depends on both engine speed (rpm) and load (vacuum). This needs thinking through in light of supercharged operation.
|
|
|
Logged
|
|
|
|
Harv
|
 |
« Reply #267 on: November 01, 2014, 05:47:41 PM » |
0
|
So just how much advance do we need for our Norman-blown grey, and how do we set it up? Our first option (Option 1) is to rely on flywheel and mechanical advance alone, and set them up so that they do not offer too much advance as boost increases. From Supercharge!, we can see the following advice: a) For every degree of “effective compression ratio” increase, retard the timing by 3º (for example, an engine on 9:1 might require 40º advance at peak r.p.m., whilst the same engine on 12:1 would only require about 32º). “Effective compression ratio” is a calculated number which tries to blend together an engines normal compression ratio with the “squeeze” obtained by supercharging. Effective compression ratio can be calculated as: Effective compression ratio = √((Boost+14.7)/14.7) x static compression ratio For example, a vehicle running 5 psi boost with a static compression ratio of 8.8:1 gives: Effective compression ratio = √((5+14.7)/14.7) x 8.8 = 10.2 Note that Weiand use a different formula: Effective compression ratio = (Boost/14.7+1)x static compression ratio This gives a different result to Eldred’s method (for example, our 5 psi/8.8:1 vehicle would return an effective compression ratio of 11.  . The difference in calculation is something to be mindful of (for example if the effective compression ratio table in the Weiand Supercharger Installation Instructions Part A are used). b) Undertake the timing reduction by reducing centrifugal advance, not by reducing flywheel advance (i.e. by regraphing the distributor, not by rotating the distributor). c) Retard the distributor itself approximately 4º in addition to allow for decreased octane. An additional set of advice is given by Weiand: “We have achieved our best results with 12 to 20° of initial lead with a total lead of 32 to 36°. The advance should be in by 2,000 to 2,500 rpm... We have found that for all of the engines that we have dyno-tested, that the best power is obtained with 32° of total spark advance, with the entire advance coming in by 2,800 rpm. This is the maximum power with 108-octane race gasoline. You will probably not be able to use this much advance with pump gasoline. Our tests have shown that dropping the total spark advance back to 25° results in a loss of only two percent of power and torque up to 4,000 rpm and four percent of power and torque at 5,500 rpm. For this small loss in power, there will be a considerable reduction in detonation.” - Weiand Supercharger Installation Instructions Part A. Weiand’s advice is consistant with guidance from other sources, for example: “For most applications, the distributor should have a centrifugal advance mechanism set up so that the entire advance is in by 2,500 rpm. Typically, 34 degrees should be a safe level of ignition lead to provide close to optimum performance.” – Chevy High Performance Magazine We can cross-check the Weiand guidance against Eldred’s views. If we take a grey motor running 7.25:1 static compression and add 10psi of boost to it, Eldred calculates Effective compression ratio = √((10+14.7)/14.7) x 7.25 = 9.4 This is an increase of (9.4 - 7.25 = ) 2.1 degrees of compression, to which Eldred would recommend (2.1 x 3 = ) 6½ degrees of centrifugal advance timing reduction, plus up to 4º of static advance reduction. Our factory grey motor running flat-out has 32º of centrifugal advance, which we would reduce to 25½º. We also have 2º at the flywheel which would be reduced by around 4º, giving a total of 23½º total advance. This is pretty close to the guidance given by Weiand (around 25º total advance). As an interesting aside, early VW’s typically started with timing of 10º flywheel advance, and around 26º of vacuum advance (no mechanical) to give 36º total. This was tuned for the Judson supercharger by reducing flywheel advance by 5-7½º to give 28½-31º. This is again similar to Weiand’s advice. So as a practical guide for setting up supercharged timing for a grey motor under Option 1, the following is a starting point: a) Disconnect the vacuum advance and plug off the inlet manifold connection. b) Regraph the distributor to give the following centrifugal advance, all-in at 2500rpm: 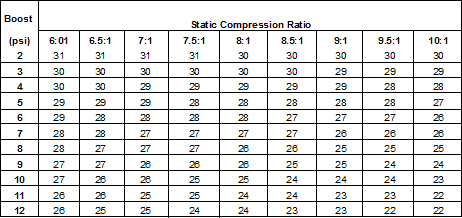 If you are unsure as to your compression ratio (say because the head has been worked) or boost level, then aim for 25º centrifugal advance, all-in at 2500rpm, c) Set flywheel advance at 2º, and reduce/advance as necessary (probably 1-4º) to reduce knocking. Option 1 is thus dependant on a particular engines boost/compression, but in summary uses no vacuum advance, changes mechanical advance from “28-32º all-out at 3450rpm” to (roughly) “25º all-out at 2500rpm” and tunes using the flywheel advance.
|
|
|
Logged
|
|
|
|
Harv
|
 |
« Reply #268 on: November 01, 2014, 05:48:23 PM » |
0
|
Our second option (Option 2) is to try to get full advantage of the mechanical advance, yet reduce timing as boost increases. We could do this with an electronic boost retard box, though this is not too period-correct. One way to do this is to utilise boost retard in a manner similar to vaccum advance (i.e. by rotating the breaker plate inside the distributor - kinda like vacuum advance in reverse). This is not as simple as just connecting up the factory Holden grey motor vacuum advance unit to boost pressure due to the internal configuration of the unit. As can be seen from the diagram below of the factory unit, vacuum acting on the green diaphragm causes a compression spring to compress, pulling on the rod to advance timing. Adding boost to the factory grey motor unit tries to make the spring stretch, bottoming out the unit. 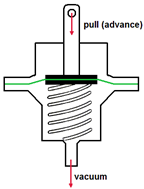 What we are looking for instead is a setup similar to that shown below. 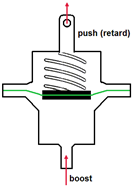 As an aside, this type of boost retard should not be confused with vacuum retard where timing is retarded with increasing vacuum, not boost. Vacuum retard is an evil process used as an emissions control device (lowering NOX emissions by dropping combustion temperature) in vehicles like the 1971-1976 Triumph TR6 and 1969-74 Jaguar Series ll and XJ6. As an example of a vehicle that did use the type of boost retard we are looking for, Chevrolet released the Corvair Spyder from 1962 with a 150hp turbocharged option. This vehicle did not use vacuum advance, but instead used a similar type of diaphragm module to measure boost. As boost increased, timing was decreased. Timing for the Corvair Spyder was as follows: a) Flywheel: 24º b) Centrifugal: 10-14º all in at 4500rpm c) Boost retard: 7.5-10.5º per psi, all in at 1.5-2.5psi. Thus a Corvair Spyder motor operating at 4500rpm and 2.5psi boost would have ignition timing of 24+10-11 = 21-23º. This is pretty close to the guidance given above by both Weiand and Eldred. In Supercharge!, Eldred mentions this type of boost retard unit, indicating: “It is difficult to get the correct spring tension and amount of travel correctly balanced with the boost pressure. However for those interested in trying this a total movement of the plate mounting the points, in the region of six degrees of the distributor will cope with an eight pound supercharge. The distributor itself will have to be advanced about eight degrees over the normal setting to compensate for the total loss of what was formerly the vacuum advance mechanism.” In summary, Option 2 uses factory mechanical advance, reduces timing with increasing boost, and tunes with flywheel advance. Without using a boost retard box, Option 2 is not an easy one to pursue.
|
|
|
Logged
|
|
|
|
Harv
|
 |
« Reply #269 on: November 01, 2014, 05:49:02 PM » |
0
|
Option 3 is a simplistic version of Option 1, and is used by many race vehicles. This involves locking the distributor. Locking the distributor means that both the vacuum advance and flywheel advance are disabled, and all timing is done by changing the flywheel advance. The advance/static compression ratios shown for Option 1 can be used (or the simplistic 25º advance used as a starting point). Locking the distributor makes it’s operation more simple (and hence more reliable), though means that all the advance the car needs comes on at very low rpm and is fixed. This is OK for a car that runs flat-out all the time (like speedway or drag cars), but not so good for cars that operate over a wide range of speeds and loads (like your typical road car). At low rpm, a fixed-timing road car can perform quite poorly. Another drama of fixed timing is that it gives waaaaaay too much advance at startup compared to a “normal” engine. When cranking over the engine, the engine may fire the charge early (especially if the engine is hot), making the piston push backwards. This can break teeth from the starter or ring gear. One way around this is to install an ignition isolation switch inside the cabin, in parallel to the factory Holden key-switch. Turn the ignition isolation switch to off (ignition off, no spark) until the motor is cranking over strongly (2-3 seconds) then flip the ignition system back on. In summary Option 3 is simple and reliable (lock the advance at roughly 25º)… just not well suited to anything that runs other than flat-out the whole time.Whilst the above deals with mechanical and flywheel advance, we also need to think about vacuum advance. Opinions vary greatly as to the need for it in supercharged vehicles. For example: a) Moss and Judson both recommend using vacuum advance with their superchargers, b) Holley (Procharger) provides for a vacuum advance connection in their supercharger manifolds, c) Several of the MSD Ignition boost retard units allow for programmable vacuum advance, and d) Shorrock disconnected vacuum advance with their superchargers. Generally, the supercharged engine will still develop vacuum (not boost) under cruise conditions, and vacuum advance can be useful for throttle response and fuel economy. Our first option for vacuum advance is to simply disconnect the vacuum advance and block off any connection on the inlet manifold. This is simple and cheap, though does sacrifice some throttle response and fuel economy. Alternatively, we can look at There are two positions we can take our pressure/vacuum signal from: a) Ported vacuum – this is taken upstream of the carburettor(s) butterfly and will always be vacuum (never pressure), or b) Inlet manifold – this is taken between the supercharger and the cylinder head, and will vary from vacuum to pressure depending on engine load. 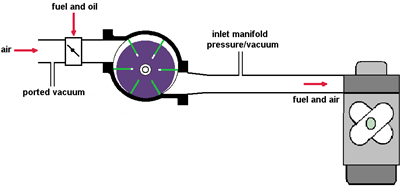 The two different locations will vary in pressure/vacuum as follows: 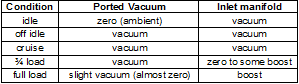 Note that this will vary slightly with configuration – for example if the carburettor is too small, then vacuum will be higher (lower pressure) at the inlet manifold but lower (closer to zero) at the ported vacuum connection. If the standard ported vacuum connection location is used to set the timing, the distributor will still see vacuum under off-idle and cruise conditions (and advance the timing) – no harm there. However, as engine load (and hence boost) begins to increase, the distributor will continue to see vacuum, increasing timing (by up to 18º for a standard grey motor vacuum unit and distributor!). Advancing the timing with increased boost will cause substantive knocking. Vacuum advance can be plumbed into the inlet manifold. In this location, the unit will see vacuum under off-idle and cruise conditions (and advance the timing). As engine load (and hence boost) begins to increase, the distributor will see boost (an absence of vacuum) and will reduce the (vacuum) timing advance to nil. The problem in doing this though is that at idle the distributor sees vacuum and retards timing. This can give a significant bog when you first put your foot down.
|
|
|
Logged
|
|
|
|
Harv
|
 |
« Reply #270 on: November 01, 2014, 05:50:16 PM » |
0
|
Whether or not we choose to use vacuum advance, we may wish to check the mechanical advance curve. Without putting the distributor on a regraphing machine, you can check the mechanical advance curve by marking the flywheel. The normal process for setting ignition timing utilizes a timing light. The light is connected to cylinder #1, and the engine allowed to idle at 480-520rpm. At this speed, a typical Holden grey motor should have zero (at most 1º) mechanical advance. Early Holdens were designed to run timed spark vacuum (the vacuum port connection is at the throttle body above the throttle plate), giving no/little signal to the vacuum advance module at idle (and hence no vacuum advance). Thus at idle we are really only checking the flywheel advance. For our Holden grey motor, when the timing light flashes it is aimed at the timing ball on the flywheel. The ball is located at 2º flywheel advance (note that the flywheel also has a “UC” mark a little anti-clockwise, which marks Top Dead Centre, or 0º advance). So our timing light is really checking that we have 2º of flywheel advance in our standard grey motor. The grey motor flywheel ring gear has 113 teeth (roughly 1/3 of a tooth per degree). Thus if we flash the timing light at more than 3450rpm, the dizzy should have advanced the timing 28-32º, or 9-10 teeth clockwise. To check the advance, put a series of coloured dots (with paint) under the flywheel teeth e.g. 0º mechanical advance = factory steel ball. 5º mechanical advance = red paint dot = 1.5 teeth to the right (clockwise) of the factory steel ball. 10º mechanical advance = blue paint dot = 3 teeth to the right of the factory steel ball. 15º mechanical advance = white paint dot = 5 teeth to the right of the factory steel ball. 20º mechanical advance = green paint dot = 6 teeth to the right of the factory steel ball. 25º mechanical advance = yellow paint dot = 8 teeth to the right of the factory steel ball. 30º mechanical advance = purple paint dot = 9 teeth to the right of the factory steel ball. You can then run the car up to a given rpm, flash the timing light and see how much advance you’ve got by looking at what coloured dot is illuminated.
At some stage I’ll come back to ignition timing and post more – I currently know how to simply limit vacuum advance, but want to play around a bit more with mechanical advance in the standard GMH dizzy. The aim is to give a simple, no welding, backyard way to setup the dizzy for a supercharger. Watch this space.
Cheers, Harv (deputy apprentice Norman supercharger fiddler).
|
|
|
Logged
|
|
|
|
Harv
|
 |
« Reply #271 on: December 20, 2014, 04:34:22 PM » |
0
|
Ladies and gents, In this post I will add some of the fiddly bits and pieces I have learnt in the last month in finishing up the Type 65 Norman rebuild. Some time back I took a good look at drive pulleys and posted the results here. My original intention was to use a GMH red motor twin pulley as a drive pulley. These will bolt to the aftermarket grey motor harmonic balancer using the three “remover/puller” holes. I bought two GMH pulleys, bolted one of them up OK, pulled it off, cleaned and painted it… must have handled the two pulleys a dozen times. I need my eyes checked. Would you believe it, the GMH pulleys are two different groove sizes. For example, one groove is 5.25” diameter, the other 5.10” (the other pulley I have is 5.23” and 5.09”). Doesn’t sound like much (and hard to see by eye unless you are looking for it). However, for our use as Norman supercharger twin-pulley drives they are not suitable. Connecting two different drive pulley groove diameters to the driven pulley (same groove diameter) puts the pulleys into bad conflict. One belt would slip badly. For example, on the 5.25”/5.10” pulley, at idle the belt would slip 8” every second, and at full noise 80”. Way too much. I guess GMH only ever drove two different accessories (e.g. airconditioning and power steering) and never ran them as a twin belt. To solve the drama, I have bolted up an alluminium twin pulley from a Chev (eBay special). It took some machining to fit, but at least is now the same pulley diameter (trust me… I measured it repeatedly). The bad thing about using Chev pulleys though is that the internal bore is much larger than the grey motor crankshaft (the Chev is 1.1” versus the 1” grey motor crank). This means it can be quite hard to centralise the Chev pulley onto the grey motor crank. I tried using one of the harmonic balancers as a template, and even taking quite some care could not get the three holes drilled perfectly concentrically. If using the Chev pulley it is recommended to either get a hub centric ring made up (a washer 1” ID and 1.1” OD), or to have the three mounting holes professionally drilled by a machine shop (3/8-24UNF on a 213/16” (71.44mm) PCD). Note when buying a Chev pulley that you will typically want one that lies very close to the harmonic balancer (rather than the “long water pump” type that stick out further). A Speedmaster PCE239.1008 item is not a bad choice ( http://store.speedmaster79.com/). The Chev drive pulley is 5.457” diameter, giving this particular Norman a drive ratio of 1.23:1. A fair amount of overdrive, though suitable for the Type 65. With a 6,000rpm practical redline on the Norman, this will impose a redline of no more than 4800rpm on the engine. With the drive pulley sorted, I turned my attention back to the idler. From my previous posts, we identified that the Kilkenny Castings KC160 was a suitable candidate to run on the back side of a double vee-belt setup. These are intended as replacement idler pulleys for VN-VP Commodores. The bearings on the KC160 are a weird unit – 40mm OD and 17mm ID. The 17mm internal diameter is painful, as it is nigh-on impossible to buy an M17 bolt to act as a pulley spindle. One option that is useful is to replace the bearing with a 40mm OD/19.05mm ID bearing (bearing part number 6203-¾). These are an oddball bearing, with a metric OD and ¾” imperial ID. This would allow you to use a ¾” high-tensile bolt as the pulley spindle. In this case, it was easier to machine the existing spindle down to ¾” (and no… I couldn’t machine down to 17mm and use the existing bearing as the spindle threads clashed). Many thanks to Cooper for helping with the machining on this one – very much appreciated.
|
|
|
Logged
|
|
|
|
Harv
|
 |
« Reply #272 on: December 20, 2014, 04:34:57 PM » |
0
|
With the idler pulley sorted, I shimmed out the pulley spindle with some washers to align the pulleys and then chose belts. I ended up using two 11A1385 belts. This is the longest belt that the setup can handle, with the tensioner almost making the back of the belts touch. 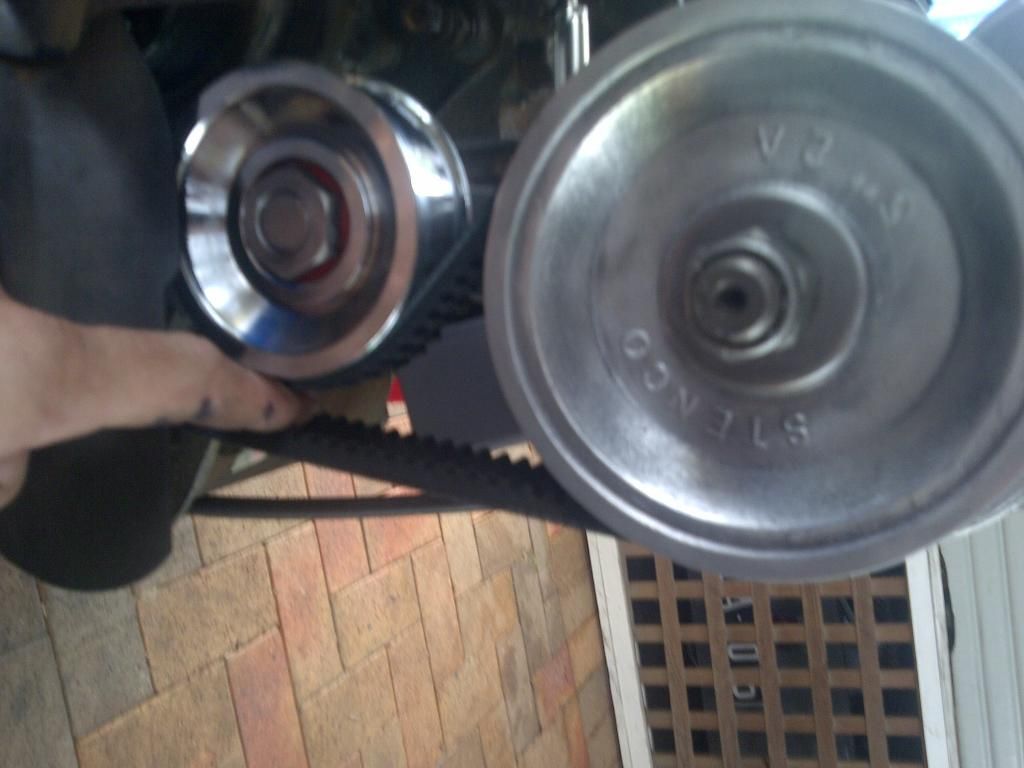 Whilst you could readily run smaller belts on this setup (for example 11A1375 or shorter), I maximised belt length to maximise belt wrap. This setup has 230º of wrap on the driven pulley, 155º on the drive pulley and 80º on the idler. These are pretty damn good values, with no need to tighten the absolute crap out of the belts to prevent slippage. The belt tensioner on this Norman has been described in earlier posts, and works by clamping on to the supercharger drive-end snout. There is potential for this clamp to slip over time, allowing the belts to lose tension. To address this, I bought a small stainless steel turnbuckle from Bunnings, which bolted to the existing idler arm (see the earlier post which shows some drilled and tapped holes on the drawing). With a little persuasion, the other end of the turnbuckle now fits to the thermostat housing bolt.  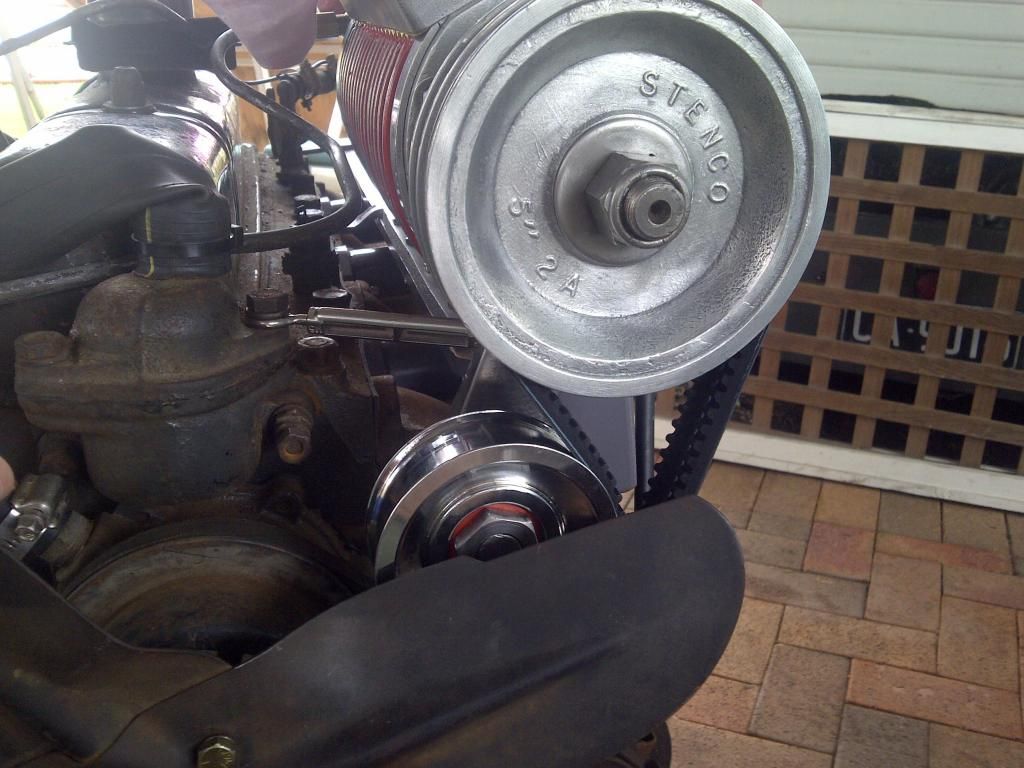 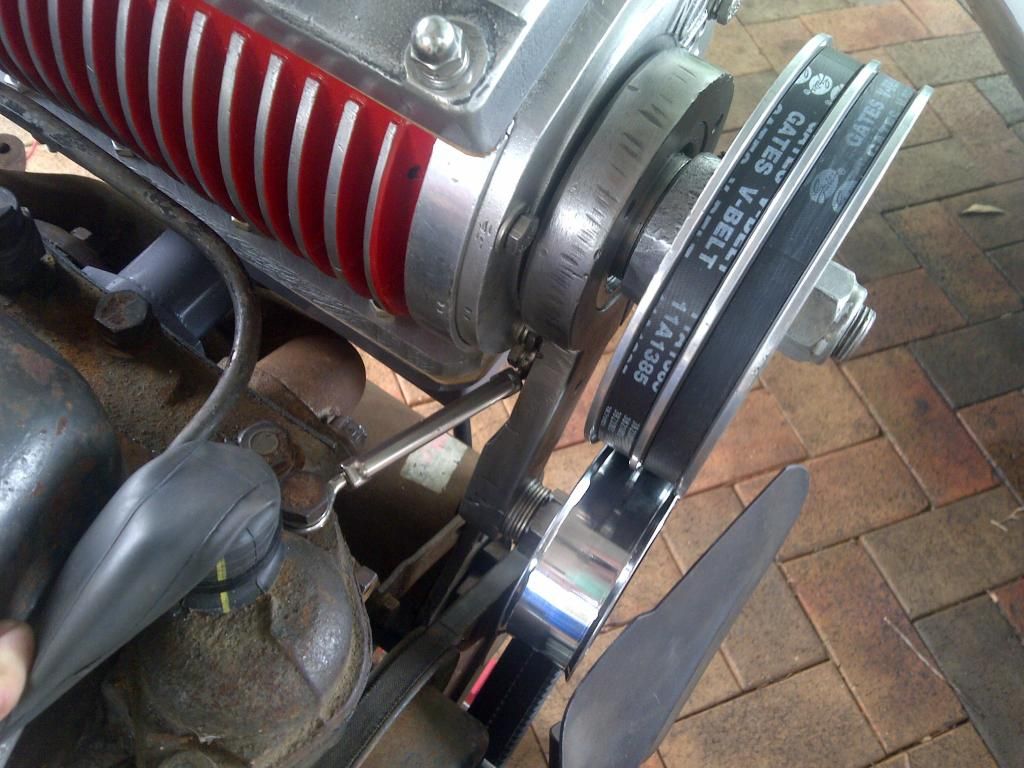 This is a very neat way to put tension on the idler, and stop it vibrating loose over time. It also means you can tighten the belts easily without trying to hold tension on the idler pulley with a long bar.
|
|
|
Logged
|
|
|
|
Harv
|
 |
« Reply #273 on: December 20, 2014, 04:35:28 PM » |
0
|
With the idler sorted, the grey motor fan became an issue. I needed to space the fan out some 1⅓” to clear the idler pulley (this gave 5mm clearance between the idler pulley and fan blade tip). A 2” thick Speco fan spacer will do the trick (part number 501707), cut down to 1⅓” thick. Be wary that the standard grey motor water pump shaft protrudes through the pulley, so the back of the cut-down spacer will need a 1” diameter hole drilled in it to suit. The standard grey motor fan bolts onto the water pump pulley with four short ¼”-28x½” UNF bolts, with some longer ¼”-28 UNFx2” bolts from SuperCheap needed. 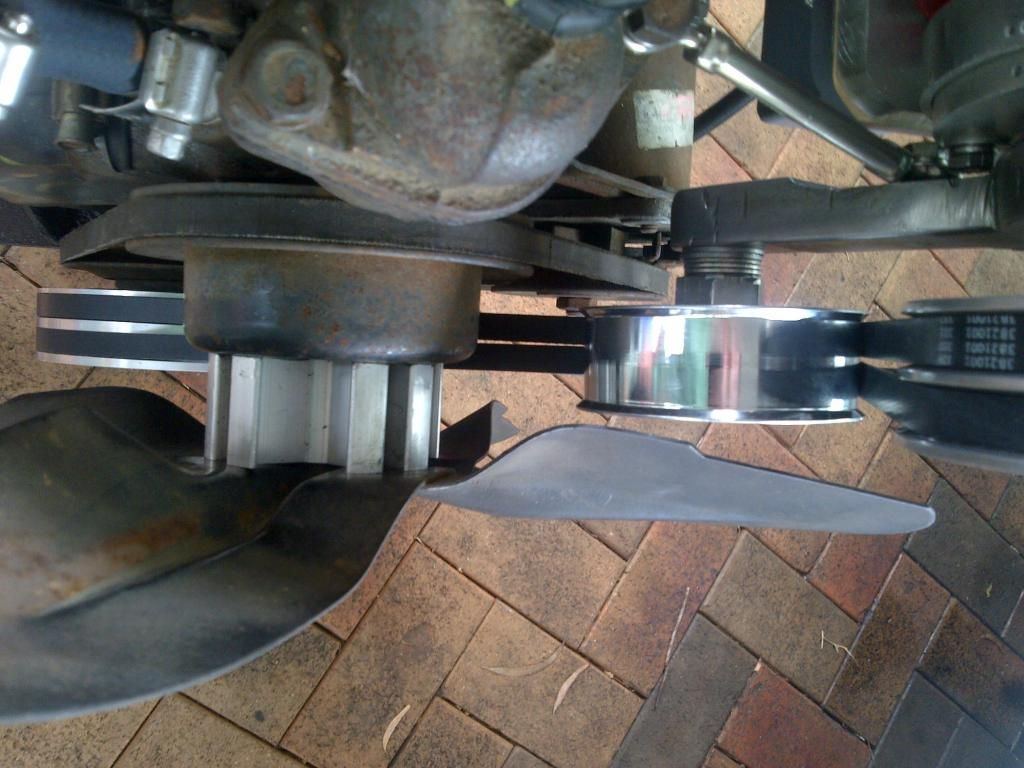 One drama here is that there is only 1” clearance between the fan and radiator in a standard FB/EK Holden - you may need to move the standard radiator forward to suit. An alternative is to run an electric fan, though this doesn’t feel too period correct. I ran some new 5/16” steel fuel line to feed the SU. As the SU has a barbed inlet fitting this needs a short length of rubber hose to join. The steel fuel line thus needs a bead rolled into the end of it to prevent the rubber hose blowing off. A simple tool to do the job is sold by Aeroflow (part number AF98-2019). 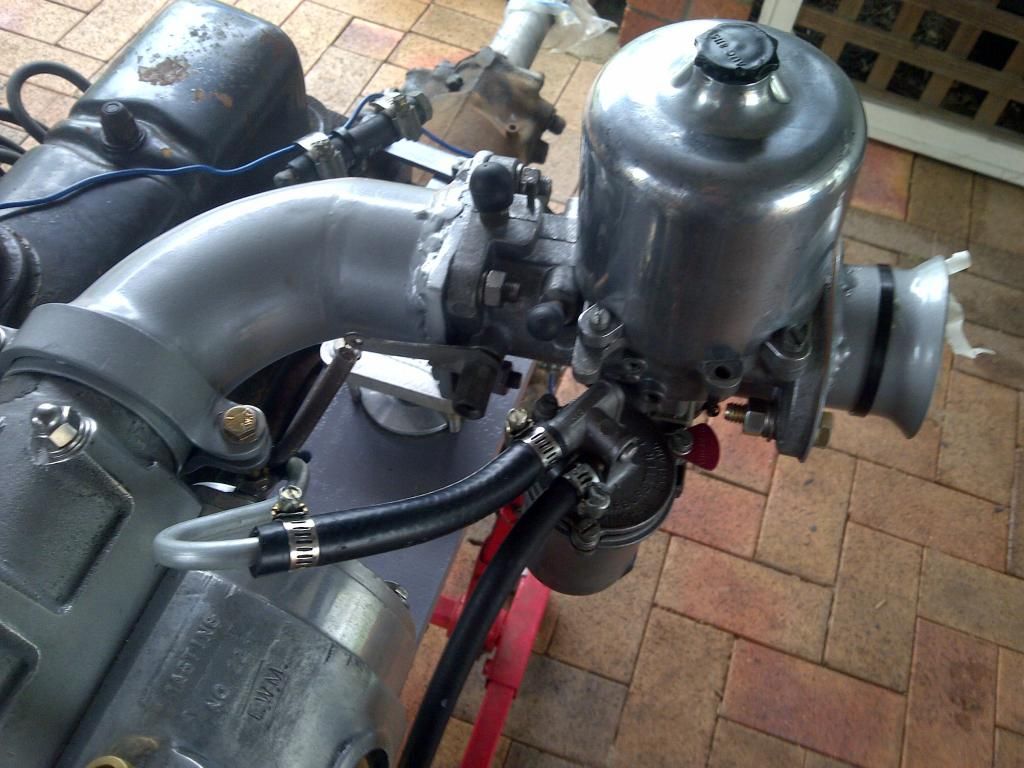 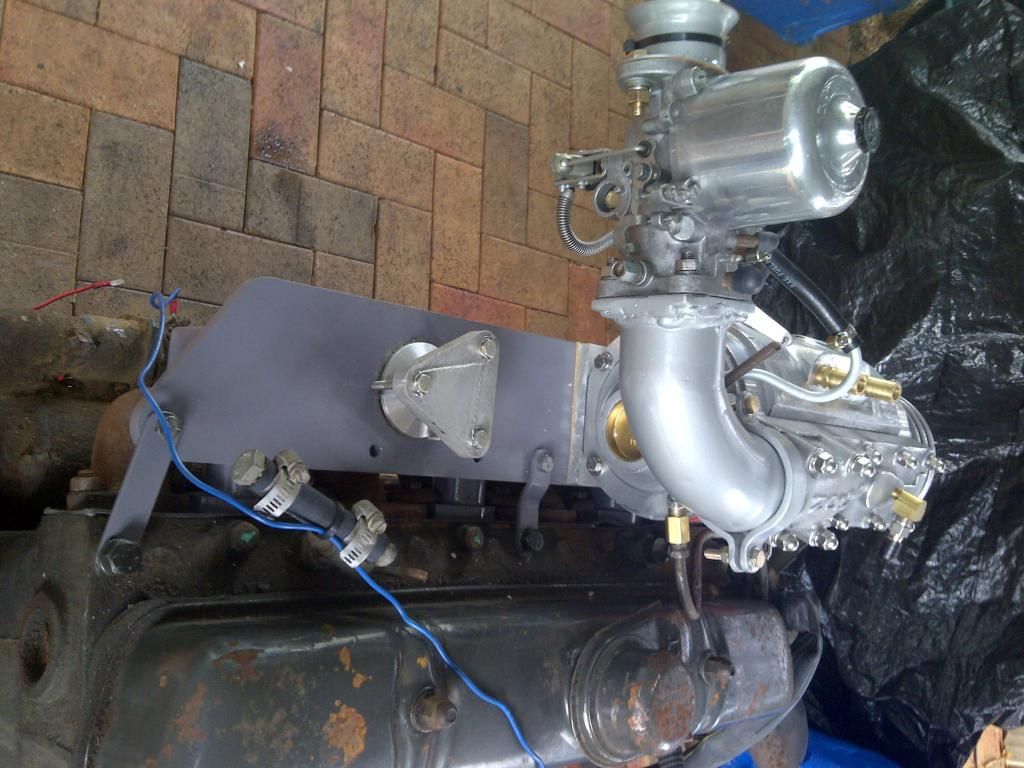 One trick here is to utilise the existing grey motor fuel line by joining it with a brass coupler (½”-20 UNF threads and a 45º double flare seat either end to suit the original 5/15" GMH fuel line). Couplers like this are available from NBS Brake Supplies ( http://www.nbsbrakesupplies.com.au/). This is handy also for anyone wanting to plumb twins or triples. 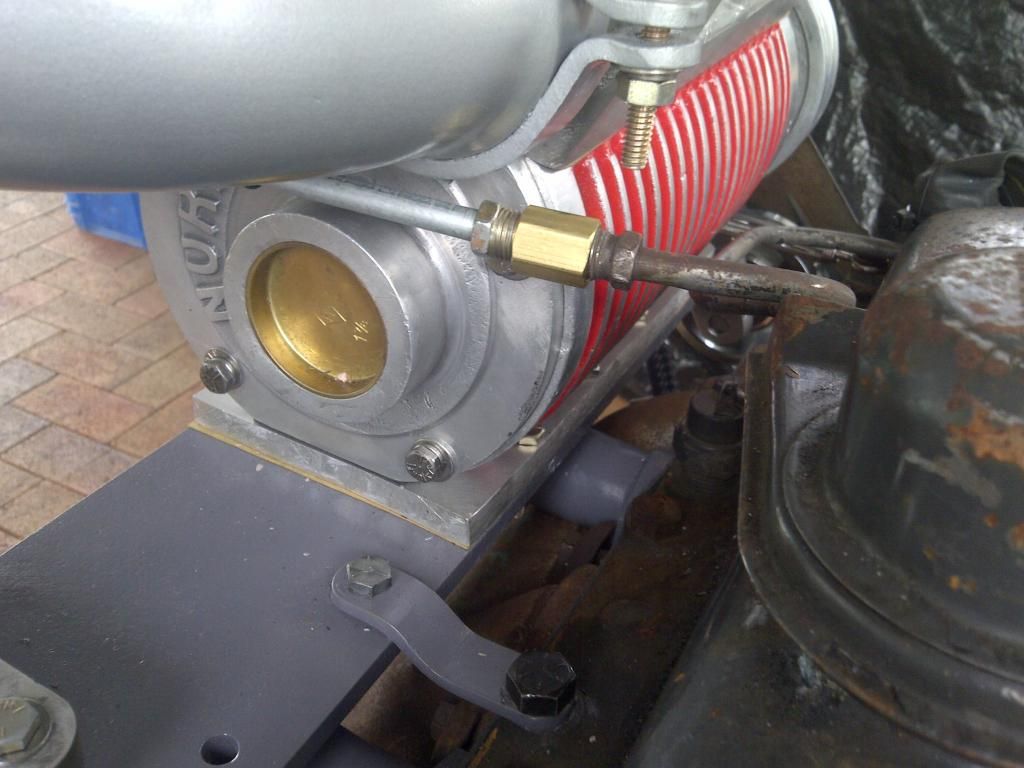 And here a photo of the near-finished Norman: 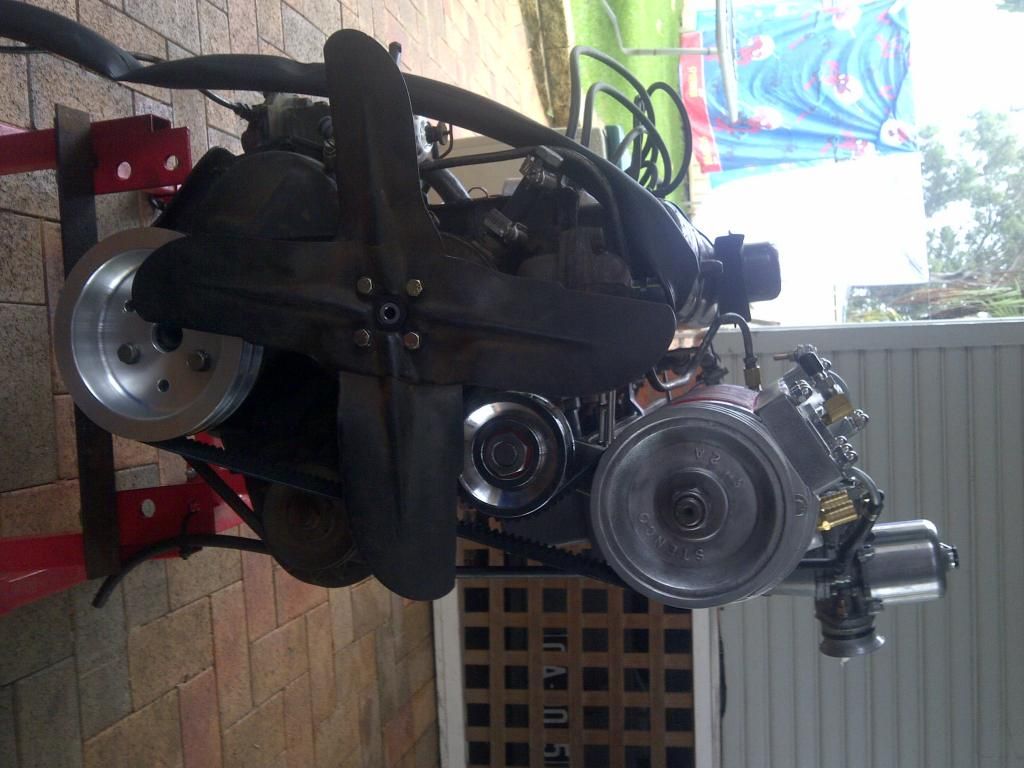 For this particular unit, my story ends here. I was pretty keen to fire it up, though the exhaust manifold I had would not allow the supercharger to fully sit square on the cylinder head. It would need some meat ground off the supercharger-to-cylinder head manifold to sit flat. As my exhaust was different to the one that will eventually go on the engine, I didn’t want to randomly grind some metal off the manifold. Even with a good sized gap in the inlet, this thing wanted to fire… the three seconds of running Norman that I got was sweet, sweet music. The Norman has now been packed up and sent back to it’s rightful owner. With a bit of luck, we’ll post some more here when it gets fired up in anger  . Next Norman project will be to overhaul one of Mike Norman's units. Similar to the Type 65 above, but some subtleties. Following that, it's probably time to tackle my clutched Type 70 (the same type as Eldred was running on his HD ute). Watch this space. Cheers, Harv
|
|
|
Logged
|
|
|
|
zulu
nsw-club
Guru
   
Offline
Model: FE and FC
Posts: 1867
Old Boonah Ambo
|
 |
« Reply #274 on: December 20, 2014, 10:10:38 PM » |
0
|
I'd like send a big thanks to Harv for all the hard work in researching, dismantling, measuring, machining, part locating, part making, assembly and finally returning the finished Norman Type 65 to me.
I would not have known where to begin and am very grateful for his offer to do all this work for me.
Thanks also to Pete FCRB26 for the manifold, it's a thing of beauty
I have started a new project, and hope to have something to share in late January, when I can get back into it
Cheers, Gary
|
|
|
Logged
|
|
|
|
fcwrangler
|
 |
« Reply #275 on: December 20, 2014, 10:22:06 PM » |
0
|
For those of us who can only dream, it would be great to have a video of the motor running and hear how it sounds. It is a good looking unit and a credit to Harv and Pete for all the work involved in getting it all set up. Jim
|
|
|
Logged
|
on the seventh day: God Made Holden
|
|
|
GreyFC
|
 |
« Reply #276 on: December 22, 2014, 08:02:43 PM » |
0
|
This pic was hurting me so I rotated it: 
|
|
|
Logged
|
|
|
|
Harv
|
 |
« Reply #277 on: January 03, 2015, 02:31:47 PM » |
0
|
A short note here on gilmer drive belts. As per the discussion above, a gilmer drive belt on a Norman supercharger is not ideal, but equally is not uncommon on the later (Mike) Norman superchargers. The gilmer belts allow for zero slippage, and can break belts (or crankshafts or supercharger rotors) during a blower bang. Assuming that your new Norman has come with a gilmer drive pulley (and perhaps a belt), the question becomes what type of belt to put on the system (or what type of pulley to buy to suit the other one). The name “gilmer” is used somewhat loosely to describe a wide variety of belt profiles. The belt manufacturing industry refers to these belts as “timing belts”, as they allow positive synchronization between two pulleys. The one thing these belts have in common is that they have teeth, which in turn mesh with teeth on the drive/driven pulleys. However, some caution needs to be taken before rolling into your local Repco store and asking for a gilmer belt. The first difference in gilmer belts is the belt profile. Gilmer belt drives are typically either trapezoidal, curvilinear, or parabolic profile. The trapezoidal profile, available since the 1940’s, is the easiest to identify. The trapezoidal pulleys and belts have flat peaks and roots, with sharp corners. The curvilinear and parabolic belts are harder to pick, as they come in a variety of configurations, including: • High Torque Drive (HTD) – a curvilinear belt introduced by Gates in 1971. • Super Torque Positive Drive (STPD) – a modified curvilinear profile introduced by Goodyear in the early 1970’s • GT – a modified curvilinear design developed by Gates in the late 1970’s and often seen in US NHRA supercharger drives in current use. • Reinforced Parabolic Profile (RPP) – a parabolic profile introduced by Dayco (Carlisle) in the mid 1980’s. The comparative profiles of the trapezoidal, HTD, STPD, GT and RPP profiles are shown below: 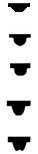 Care needs to be taken in that whilst some of the above pulley systems are compatible with each other, some will only run their belt profile on their particular pulleys. If in doubt, it is wise to take the pulley (or belt) to a power transmission company (like CBC Bearings) for identification advice. The next area in which there is quite some variation in gilmer belts is in the belt pitch. The various belt profiles have pitches as per the diagram and tables below. 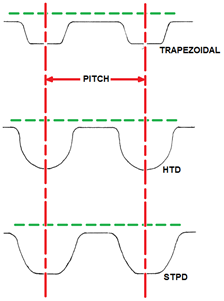 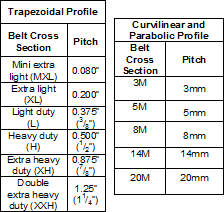 Note that the pitch distances shown above are measured on a belt, where the middle of the belt is shown by the green line (in the image below). 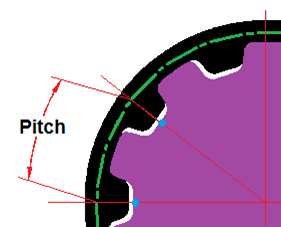
|
|
|
Logged
|
|
|
|
Harv
|
 |
« Reply #278 on: January 03, 2015, 02:33:21 PM » |
0
|
This is not quite as simple to measure on a pulley. The image to the right shows a purple pulley, running a black belt. The green line again shows the middle of the belt. When measuring the pitch of the pulley, it is measured at the middle of the belt. Measuring on the middle of the pulley teeth (where the blue dots are in the image) will give an incorrect pitch (too small). The next area that gilmer belts vary in is the belt width. Thankfully, this is a lot easier to measure than pitch, by measuring across the pulley face. Finally, like vee-belts a gilmer belt will vary in length. Some suppliers specify the belt by the circumference (similar to a vee-belt), whilst other classify belt length by the number of teeth the belt has. Whilst many of the rules for setting up gilmer pulleys is identical to that of vee-belts, some good guidance is given in A study of supercharger belt failures, National Dragster July 24 1992, and as shown by the purple arrows in the image below: 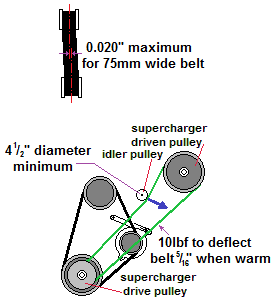 • Pulley alignment needs to ensure that pulley centers are no further than 0.020” misaligned on a 75mm drive belt. • Back tension idler pulleys should be no less than 4½” diameter to reduce bending stress on the belt. • Drive belts should be tensioned such that 10lbf is required to deflect the belt 5/16” at mid-span on the drive portion of the belt (between the drive and driven pulley) on a warm engine. Whilst a number of sources are available for drive (and driven) pulleys, one local source is Naismith Engineering ( http://www.naismith.com.au/pdf/timingpb.pdf). Engineering suppliers like CBC bearings ( http://www.conbear.com/) can provide supercharger belts in a variety of profiles and lengths. Cheers, Harv (deputy apprentice Norman supercharger fiddler).
|
|
|
Logged
|
|
|
|
customFC
nsw-club
Guru
   
Offline
Model: FC
Posts: 5904
Ask me about microwaving cats for fun or profit.
|
 |
« Reply #279 on: January 03, 2015, 07:21:44 PM » |
0
|
This is a fascinating thread Harv. Thanks for taking the time to share your knowledge. Gary - can't wait to see what you have planned for this setup. Will that carby clear an FC bonnet? Regards Alex
|
|
|
Logged
|
|
|
|
|