Harv
|
 |
« Reply #20 on: August 26, 2013, 09:57:11 AM » |
0
|
There are however some down-sides to intercooling: • the intercooler and piping have a pressure drop. This reduces boost pressure. We can combat this to some extent though by making the supercharger run a little faster (smaller driven pulley) provided we are not already at the limit of what the supercharger can produce. • the intercooler takes up additional space under the bonnet. • water/air intercoolers utilizing the cars coolant system will circulate warm water. When the car is under low load, the air passing through the intercooler may be colder than the engine coolant. In this case the intercooler acts as an “interheater”, reducing charge density instead of increasing it. • the intercooler increases the volume of the inlet system. As Norman sueprchargers are suck-through line-ups, all the inlet system contains an explosive air/fuel mixture. Increasing the volume (by adding an intercooler) increases the size of the potential explosion. To quote Eldred: “Intercoolers are not really feasible. If they are large enough to be effective they form a too large reservoir for the mixture, and when there is a backfire it is almost of nuclear proportions.”. Practically, if the Norman supercharger has an intercooler then it will probably be used, if only for nostalgia sake. If the supercharger does not have an intercooler, then one may be installed to chase additional horsepower. For those looking for a period-correct installation, or are concerned over the potential to damage the supercharger installation by explosion, an intercooler is not required. A turbo timer is an electronic device which keeps the engine running (at idle) for a period of time after you turn the key off. It does this allow low-boost, cool air to cool down the exhaust and intake tracts (remember that the turbocharger is driven by exhaust gas, and can become incredibly hot under load). At the same time the engine oil is able to circulate, preventing the red-hot turbo bearings from cooking the oil to carbon (…or melting). Norman superchargers do not suffer from the same high temperatures as a turbocharger. However, they do increase in heat under load. Whilst a turbo timer is not required, it is god practice to drive the car under low load (or at idle) for a few minutes between high load operation and shut down.
So in short: • Norman superchargers are normally suck-through line-ups. • a blow-off valve is a flow control device used to protect superchargers from surge. It is not required on a Norman supercharged vehicle. • a relief valve is an overpressure control device used to protect against explosion inside a supercharger. It is required on a Norman supercharged vehicle. • a wastegate is a rotational speed and boost pressure control device. It is not required on a Norman supercharged vehicle. • a boost controller is a device that changes how a wastegate behaves to optimize boost pressure delivery. It is not required on a Norman supercharged vehicle. • a bypass valve is a device that improves economy at low supercharger load. They are present in Deluxe Norman superchargers, but otherwise not required on a Norman supercharged vehicle. • an intercooler is a device used to get more supercharged air into a vehicle and reduce knocking. They are present in some Norman supercharger installations. Whilst they can add additional horsepower they increase the risk of explosion and are not absolutely required. • a turbo timer is a device that allows a hot turbocharger to cool down properly. It is not required on a Norman supercharged vehicle.
Cheers, Harv (deputy aprentice Norman supercharger fiddler).
|
|
|
Logged
|
|
|
|
Harv
|
 |
« Reply #21 on: September 26, 2013, 06:24:17 PM » |
0
|
One question that commonly comes up is “just how much grunt will I get from a Norman?”. In the next few posts I will take a long look at the performance of Norman superchargers. Some of this will be geeky, engineering modeling of how superchargers work (my apologies in advance for those not inclined), whilst some will be comparing factory and road test results. Whilst it is possible to install and field test Norman superchargers (the “suck it and see” approach), there are some difficulties in doing so: • There are not all that many Norman superchargers around, and the few that are available are (rightly) viewed as valuable. Convincing someone to allow you to bolt up their supercharger and then test the boundaries of it’s performance is not likely to be an easy task, • There are quite a few variables that need examining. It can be a very expensive process sourcing multiple supercharger drive pulleys (for example), let alone the time and cost of either road or dynamometer testing, • The cost of failure can be expensive. A severely knocking engine under load can very quickly lead to engine failure, and • It has been a considerable time since the Norman supercharger was built. Over the last half century, supercharging technology has increased in leaps and bounds. The increase in technology also means that our expectations of superchargers has changed. Our mental model of “normal supercharging” now includes 15 psi boost pressures, huge intercoolers and EFI. Whilst some of these expectations are applicable to Norman superchargers, many are not… or at least not when the “traditional approach” to using a Norman is desired. The modeling process involves estimating some issues (for example how efficient the superchargers are), and then calculating what the likely supercharger performance will be (power output, onset of knocking, impacts on bearing design etc). It is recognized that this process is only an estimate – the information below should not be seen as “hard and fast” rules, but rather as a guide or starting point to what these superchargers are capable of. Where I have made assumptions (for example in volumetric efficiencies) I will highlight the likely range of the value involved. In order to model the performance of Norman superchargers, we need a starting point. I have drawn the data below from the respective factory Workshop Manuals: 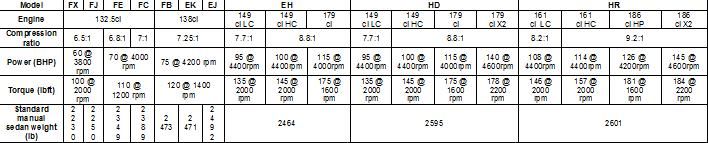 There are lots of tricky numbers in that table, so let’s make it simple by using a number that is more familiar – quarter mile time. To estimate the likely unblown performance of the above vehicles, it is possible to estimate the quarter mile elapsed time (ET) using a formula often referred to as “racer math”. The racer math formula is: ET = 5.825 x (weight/power)1/3 Where: • Elapsed time is the time for the vehicle to travel the quarter mile drag strip, and is in seconds, • Weight is the vehicle weight in pounds, and • Power is the vehicle brake horsepower. Applying the formula to the early Holdens above yields the following:  No suprises here – the Holdens get quicker and quicker with each new model, with a big change in performance when the red motor was introduced into the EH Holden.
|
|
|
Logged
|
|
|
|
Harv
|
 |
« Reply #22 on: September 26, 2013, 06:25:16 PM » |
0
|
Now that we have a starting point, the key question at this point is just how much power can be squeezed out of a Norman supercharger. As an example, we can take the following anecdote as noted in Supercharge by Eldred Norman: “In 1954, driving a supercharged Triumph TR2, I finished 4th in the Australian Grand Prix. On this car I used a “boost’ of 12lbs. The supercharger was a G.M. 271 Roots type unit operating at 1.1 times engine speed and driven by four ‘A’ section V belts. By the end of the race belt-slips had caused a fall in boost to a maximum of 8 lbs. Naturally I had to ‘nurse’ the belts by not using full throttle at this stage. My present Holden is some 50% greater in capacity than was the Triumph. I am using a 10 lb. supercharge from my type 110 vane type supercharger and drive it with only two ‘A’ section belts. Under these conditions the vane type is putting out almost 40% more air/fuel than did the Roots with twice the number of belts. Certainly the car is not being raced which is an enormous difference. But my belts last at least 5000 miles of normal road use. Detractors of the vane type supercharger have usually only seen the wrong unit on the job.” The Triumph TR2 has an engine capacity of 121ci, inferring Eldred’s Holden had a capacity of 182ci. This could be either of the 179ci or 186ci Holden red motors, allowing for rounding of numbers. If we assume that this was Eldred’s reknowned HR Holden with a 186ci motor, with a weight of 2600lb (1180kg), and a performance of 0-100mph in 14 seconds (as per the cover page of Supercharge), then we can use the estimator at the following site ( http://www.torquestats.com/modified/index.php?pid=calculator) to estimate the power as being 232BHP. The increase from the HR Holden’s naturally aspirated 145 BHP is some 60%. A power increase of around 60% seems a fair boundary for the Norman supercharger. This seems low compared to the ~100% increases that can be achieved with modern intercooled supercharging. However, bear in mind that early Holden motors (and particularly the grey motor) have fairly poor flowing cylinder heads, and a limited ability to absorb additional power without snapping cranks or smashing gearboxes, and that intercooling a Norman is no easy task (more on this later). I will use 60% in the information below. Applying the “racer math” formula but with some increased horsepower shows the following quarter mile elapsed times are probably achievable with a Norman supercharger: 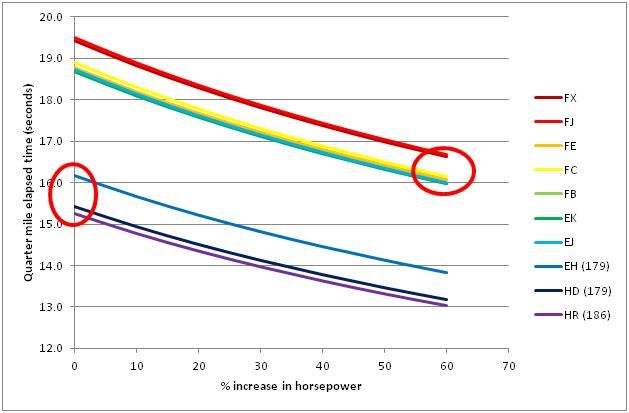 This shows that our Norman blown grey motor, pumping out an additional 60% more power, should be good for around 16 second quarter miles. Whilst not too great in comparison to modern 10-second quarter mile times, it’s not too bad considering that our 60% blown grey is probably still quite a streetable car with none of the lumpy cam, methanol slurping, high geared misbehaviour. Note the two red circles I have drawn on the graph. These show that our blown 60% grey is still only just as quick as an unblown red – a sad fact of life. This is not to say that you cannot squeeze more grunt out of a Norman supercharged grey... just that the results will be typically around the above. More on Norman power in the next few posts. Cheers, Harv (deputy apprentice Norman supercharger fiddler).
|
|
|
Logged
|
|
|
|
FC0058
|
 |
« Reply #23 on: September 27, 2013, 04:41:47 AM » |
0
|
Hi Harv Not sure how I have missed this thread but am looking forward to grabbing my glasses and having a good read. Cheers for sharing with us all threads like this one are what makes this forum and draws us car enthusiasts together.
Cheers Jim
|
|
|
Logged
|
Forgiveness is easier than permission.
|
|
|
jack_fc
Senior Member
  
Offline
Model: FC
Posts: 745
SouthWest Coast, Victoria
|
 |
« Reply #24 on: September 27, 2013, 09:43:37 AM » |
0
|
Great reading - thanks Harv! Re the 'racers math' - the theoretical 1/4 mile ETs generated from this seem very quick... (16.2 for a 179 EH  My warm 202 powered EH couldn't do that!) cheers, jack
|
|
|
Logged
|
"when I was a young lout, it was all about sex, drugs, rock'n'roll, beer and hot Holdens. Now I'm an old lout, but I've still got the old Holdens and beer..."
|
|
|
Harv
|
 |
« Reply #25 on: September 28, 2013, 12:23:03 PM » |
0
|
OK, onto some more "geeky" stuff - modelling the Norman. I have performed the calculations below in a manner consistent with the guidance in Supercharged! Design, Testing and Installation of Supercharger Systems by Corky Bell. In doing so, I have made the following assumptions: a) I have assumed that the Holden grey motor engine volumetric efficiency (VE) is 80%. • Holley Carburettors, Manifolds and Fuel Injection by Mike Ulrich indicates that ordinary, low performance engines (this sounds like a typical grey motor!) have a VE of 80% a maximum torque, high performance engines 85% and all-out racing engines 95%. • Garrett (the turbocharger manufacturer) indicates that volumetric efficiency ranges in the 95%-99% for modern 4-valve heads and 88% - 95% for 2-valve designs (whilst the grey motor has two valves, it is nowhere near contemporary). • EPI Engineering ( http://www.epi-eng.com/index.html) indicates that in general automotive engines rarely exceed 90% VE. b) I have assumed that the Norman supercharger volumetric efficiency is 90%. • From The Standard Handbook of Petroleum and Natural Gas Engineering, Volume 1 (edited by William Lyons) sliding vane compressor volumetric efficiency ranges from 82% to 90%, with 82% representing higher boost pressures. • From Compressors: Selection and Sizing by Royce Brown, sliding vane compressor volumetric efficiencies range from 90% at 10psig (a typical Norman supercharger pressure) to 85% at 30 psig (way too high a pressure for a Norman supercharger). • From The Internal Combustion Engine in Theory and Practice by C. F. Taylor, sliding vane compressor volumetric efficiency is typically 85%. c) I have assumed that the adiabatic efficiency of the Norman supercharger is 60%. • Supercharge by Eldred Norman indicates that Roots superchargers have an adiabatic efficiency of about 50%, sliding vanes superchargers 70% and centrifugal superchargers 90%. These values seem high in comparison to the numbers below. • Supercharged! Design Testing and Installation of Supercharger Systems by Corky Bell indicates that supercharger adiabatic efficiency is in the range 50-65%. d) I have assumed that the Norman supercharger drive power efficiency is 90%. Supercharged! Design Testing and Installation of Supercharger Systems by Corky Bell which indicates the following for drive power efficiency (and utilises a constant 90% for all calculations): • 5psi boost: 93%, • 10psi boost: 90%, and • 15psi boost: 86%. e) I have assumed that the Norman supercharger thermal efficiency is 65% (higher than the Roots supercharger due to the sliding vanes internal pressure ratio, but lower than the twin screw/centrifugal supercharger due to the heat generated by the vanes moving against the casing). • Supercharged! Design Testing and Installation of Supercharger Systems by Corky Bell indicates the following efficiencies: Roots supercharger: 55%, Twin-screw supercharger: 70%, Centrifugal supercharger: 75%, and Typical turbocharger: 75%. • The Internal Combustion Engine in Theory and Practice by C. F. Taylor indicates a mechanical efficiency of 65%. f) I have assumed that the ambient air temperature is 35ºC (96ºF using the normal temperature scale). This number is converted to the absolute temperature scale for the calculations below by adding 460ºF (i.e. 35ºC = 96 + 460 = 556ºFabsolute).
|
|
|
Logged
|
|
|
|
Harv
|
 |
« Reply #26 on: September 28, 2013, 12:23:34 PM » |
0
|
The calculation process is an iterative (cyclic) one – you make some initial estimates of boost, calculate the resultant supercharger outlet temperature, and then calculate boost. You feed the newly calculated boost back into the start of the cycle again, and keep cycling around until the numbers coming out are constant. For the example below, I will assume a Holden 138ci grey motor (75BHP from the factory, 7.25:1 compression ratio and 4200rpm redline) with a target of 50% power increase (say 110 BHP) once supercharged. I will model the small Norman (82.79 inch3/revolution).
First iteration – this will allow us to make a first guess of the boost required, and how hot the air will be leaving the compressor. 1. Volumetric efficiencies ratio = (supercharger VE/engine VE) = (90/80) = 1.125 (this number will remain constant throughout the calculations). 2. Pressure ratio = (desired horsepower/existing horsepower) = (110/75) = 1.47 (this number we will keep calculating/updating in the iteration cycles below). 3. Boost = (pressure ratio – 1) x atmospheric pressure = (1.47-1) x 14.7psi = 6.91psi (this number is our first guess of the boost required, and will change as we will keep calculating in the iteration cycles below). 4. Drive power efficiency = -0.7 x boost + 96.667 = -0.7 x 6.91 + 96.667 = 91.8% (this number we will keep calculating/updating in the iteration cycles below). 5. Temperature gain across the supercharger = ((pressure ratio^0.28)-1)xTabsolute/thermal eficiency = ((1.47^0.28)-1)x556/0.65 = 97ºF (this number is our first guess at the temperature rise that the supercharger imparts to the air that it is compressing, and will change as we will keep calculating in the iteration cycles below).
Second iteration – this will let us update our estimate of boost and outlet temperature. 1. Density ratio = supercharger inlet temperature/supercharger outlet temperature = 556/(556+97) = 0.851 (this number we will keep calculating/updating in the iteration cycles below). 2. Pressure ratio = desired horsepower/(existing horsepower x densiy ratio x volumetric efficiencies ratio x drive power efficiency) = 110/(75x0.851x1.125x0.918) = 1.669 (this is our second guess at the pressure ratio). 3. Boost = (pressure ratio – 1) x atmospheric pressure = (1.669-1) x 14.7 = 9.83psi (this is our second guess at the boost pressure required). 4. Drive power efficiency = -0.7 x boost + 96.667 = -0.7 x 9.83 + 96.667 = 90% (this number we will keep calculating/updating in the iteration cycles below). 5. Temperature gain across the supercharger = ((pressure ratio^0.28)-1)xTabsolute/thermal eficiency = ((1.669^0.28)-1)x556/0.65 = 132ºF (this is our second guess at the supercharger temperature increase).
Third iteration – again updating our estimate of boost and outlet temperature. 1. Density ratio = supercharger inlet temperature/supercharger outlet temperature = 556/(556+132) = 0.808 2. Pressure ratio = desired horsepower/(existing horsepower x densiy ratio x volumetric efficiencies ratio x drive power efficiency) = 110/(75x0.808x1.125x0.90) = 1.79 3. Boost = (pressure ratio – 1) x atmospheric pressure = (1.79-1) x 14.7 = 11.6psi (this is our third guess at the boost pressure required). 4. Drive power efficiency = -0.7 x boost + 96.667 = -0.7 x 11.6 + 96.667 = 88.5% (this number we will keep calculating/updating in the iteration cycles below). 5. Temperature gain =((pressure ratio^0.28)-1)xTabsolute/thermal eficiency = ((1.79^0.28)-1)x556/0.65 = 151ºF (this is our third guess at the supercharger temperature increase).
If we keep iterating around and around again (Microsoft Excel is great for this), the numbers in our example finally stabilise as follows: • Boost = 12.9psi • Pressure ratio = 1.47 • Temperature gain = 165ºF
I'll run some more numbers and show what this means for our small Norman in the next post.
Cheers, Harv
|
|
|
Logged
|
|
|
|
NES304
|
 |
« Reply #27 on: September 28, 2013, 10:18:16 PM » |
0
|
Wow mate, REALLY good work. Such an interesting thread.
|
|
|
Logged
|
|
|
|
Harv
|
 |
« Reply #28 on: October 01, 2013, 08:24:14 AM » |
0
|
So what do we do with this supercharger calculation process? Firstly, it gives us a useful tool for looking at what happens as we wind up the boost on a Norman. Taking our blown grey example above and running a few different power levels through it lets us generate the example chart below: 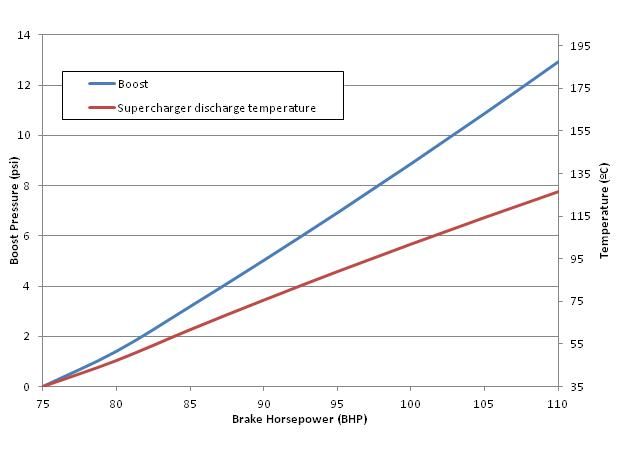 So what does the chart tell us? Firstly, along the bottom of the scale is the engine horsepower, starting at the factory 75BHP. As we wind boost up from zero to 13psi, our power output increases up to around 110BHP. From earlier discussion, we know that the early supercharged grey motors were not high boost machines, which is why I stopped the calculations here. If we look for our “typical” 50% or so power increase, we would need to be at the 13psi level. This seems a little high compared to the 5psi or so the old blown greys were running, but is in the right ballpark. So why does the model give 13 and not 5? We need to think a little bit more about this – it is largely temperature related.
|
|
|
Logged
|
|
|
|
Harv
|
 |
« Reply #29 on: October 01, 2013, 08:25:10 AM » |
0
|
The secondly thing we can see from the graph is the supercharger discharge temperature. We can see that the supercharger discharge temperature rises with boost, up from ambient at zero boost to about 125ºC at our 110BHP. This is again directionally correct. Looking at some of the literature: “Even with low boost pressures, manifold temperatures easily reach the 300 degrees (150ºC) mark, or even higher when driving a supercharged car at sustained high speed on petrol” - Blow for Go! Australian Hot Rod November 1966. This shows our estimate of output temperature is in the right ballpark. So why does the boost pressure in the model seem so high? One of the big issues is that the model (correctly) assumes we are not running an intercooler – discharge temperature increases dramatically with boost. This is a bit different to a modern supercharged (or turbocharged) vehicle with a thumping great intercooler hanging out of the front bumper. That high supercharger discharge temperature means our nicely compressed air/fuel mix is getting hot and less dense... bit of a shame to lose some of the density we were hoping to achieve by supercharging. Worst still, high supercharger discharge temperatures can lead to knock. The historic grey motor set-ups were often run with water (or water/methanol mixture) injection as a knock-inhibitor. Water does this by reducing the temperature of both the inlet system and combustion chamber. We know from the same article above that the 110 Deluxe Norman supercharger kits were introducing water from 110ºF (43ºC), and keeping temperature within 10ºF (say 43ºC – 49ºC). The use of water to cool things down is not counted for in our above model, which is why boost pressure seems so high. Modelling water injection and it’s effect on boost temperature can be complex, mainly because water injection does some funky things inside the combustion chamber – there is a combination of: a) Lower temperature due to the vapourisation of water, and hence higher charge density (more fuel and air gets in), b) Less fuel and air being introduced because some is replaced by water (which doesn’t burn too well), c) Changes in combustion chemistry due to the interaction of water molecules with fuel during the chemical burning process, and d) A “steam turbine” effect as some of the unvapouised water flashes off with increased heat. Modelling all the above is damn hard – you would need to be a rocket scientist. We can however model just the simple “lower temperature” part. For example, we can model what would happen if we were able to keep the supercharger outlet temperature at say 50ºC (i.e. run a Norman with water injection similar to the 110 Deluxe injection system). To do this, we perform the same calculations as the example above, but when we calculate density ratio: Density ratio = (supercharger inlet temperature)/(supercharger outlet temperature) We use 50ºC (122ºF or 582ºFabsolute) instead of the calculated (and much higher) supercharger outlet temperature. Running this process through for our “small Norman blown grey” example above gives the following chart: 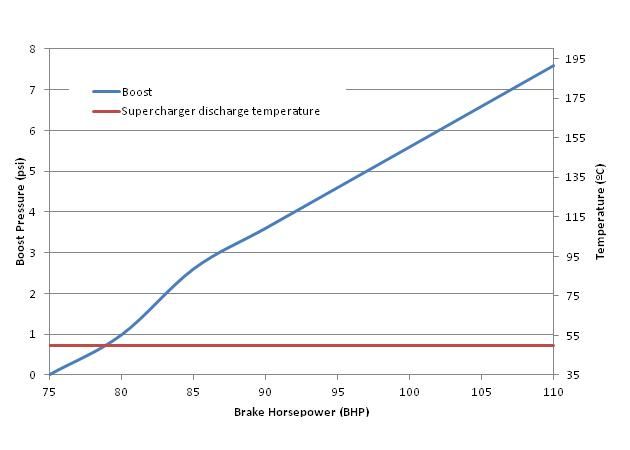 This graph looks more familiar – our 50% power increase is now in the 7½ psi or so range. The above gives us some confidence that the model is not too bad, bearing in mind that the accuracy is probably only +/- 1psi on boost pressure. The model could do with some tuning against dyno data, but as we noted above convincing someone to allow you to bolt up their supercharger and then test the boundaries of it’s performance is not likely to be an easy task. One set of data that is available is from the same Australian Hot Rod article noted above. In the article, Eldred notes that a standard 179ci motor generates 69BHP at 3,000rpm and 115BHP at the 4,000rpm redline. The latter value indicates that this is probably the HD Holden 179 (this is backed by the article also referencing a 179 X2 engine, as per the HD Holden). We can assume then that the engine volumetric efficiency has increased a little bit over our asthmatic grey motor... say from 80% to 85%. The article indicates that at 4500rpm, the supercharger is putting at 7psi and the motor is developing 145BHP. If we run these numbers through the model, it predicts that Eldred’s blown 179ci at 145BHP will require 6.7 psi with no water injection, or 5.8psi with a 122ºF water injector. This is pretty close to the numbers noted in the article, given the accuracy of the data. I know the last few posts have been a bit geeky  . In the next few we’ll take a look at how we can use the modelling more usefully – predicting pinging, making choices about water injection and sizing pulleys. Cheers, Harv (deputy apprentice Norman fiddler).
|
|
|
Logged
|
|
|
|
fcwrangler
|
 |
« Reply #30 on: October 01, 2013, 06:59:54 PM » |
0
|
Harv, have you seen the old supercharger on ebay at the moment, listed as a Norman but does'nt look like it. Current bit $260, listed in fc holden page 1. Jim
|
|
|
Logged
|
on the seventh day: God Made Holden
|
|
|
Harv
|
 |
« Reply #31 on: October 02, 2013, 06:53:57 AM » |
0
|
G'day Jim,
Yep, I've seen it (one of the EJ/EH forum guys pointed it out a few days ago). The comments down the bottom of the eBay listing are mine - pretty sure it's not a Norman. The "siezed" part is a worry, as the end plates may warp getting them off the bearings if they are too stuck.
Cheers, Harv
|
|
|
Logged
|
|
|
|
Harv
|
 |
« Reply #32 on: October 02, 2013, 06:42:07 PM » |
0
|
One issue that our model is useful for is to look at knocking (pinging. There are a number of different views as to when the onset of pinging occurs. Weiand ( http://www.holley.com/data/Catalogs/Weiand/68.pdf) calculates the supercharged engines effective compression ratio as: Effective compression ratio = (boost/14.7 + 1) x static compression ratio. Warning... this is not the only way to calculate effective compression ratio – just the one Weiand has chosen (more on this later when we talk about timing). Weiand has found that for Rootes type superchargers, running 92 octane fuel, with no intercooling and with no ignition retard that pinging will not occur with an effective compression ratio lower than 12:1. 92 octane fuel is a little low given that 98 is freely available in Australia. We this need to temper Weiand’s rule of them a bit. One way to do this is to use the rule developed by A K Miller (a US salt lake racer and manufacturer of turbocharger kits, see Turbochargers by Hugh MacInnes). Miller’s view indicates that the octane required of an engine increases by one point for every psi of boost (for example a 90 RON naturally aspirated engine requires 98 RON at 8psi boost). This is slightly less conservative than the rule of thumb developed by both Kenne Bell (a US manufacturer of superchargers - http://www.kennebell.net/KBWebsite/FAQ_pg/layouts/faq-answers1.htm) and Corky Bell (see Supercharged! Design, Testing and Installation of Supercharger Systems), both of whom indicate that 1½ octane points are required to support one psi of boost. If we use the more conservative 1½, then we can bring together the Weiand and Miller/Bell/Bell’s experience to draw the chart below:  The range of compression ratios seen in factory Holden grey motors is 6.5:1 to 7.25:1, whilst for EH-HR Holden red motors is 7.7:1 to 9.2:1. The graph shows that for our grey motor running on 98 RON we should be able to achieve 14 to 16psi of boost without pinging. Sense checking this information: • “Typically, a 5- to 8-psi boost range (usually produced with the supplied pulleys in blower kits) will work fine for compression ratios in the 8:1 to mid-9:1 range (operating on 91/92-octane fuel).” - Chevy High Performance Magazine. This advice is in the same ballpark as the above graph, but a little less conservative. • “For carburetted engines with compression ratios of 9:1 or less and boost levels in the 8-14 psi range, pump gasoline works very well. Compression ratios of 10:1 and higher require lower boost levels, higher octane fuel, intercooling, or some combination of the above. Compression ratios in the 7 or 8:1 range can usually handle 12-20 psi on pump gasoline.” – The Supercharger Store. This advice is again in the same ballpark but less conservative.
|
|
|
Logged
|
|
|
|
Harv
|
 |
« Reply #33 on: October 02, 2013, 06:42:40 PM » |
0
|
Whilst the data above is a good guess, it is pretty rough and based on multiple rules of thumb. To be honest, it is probably a little too rough to be really useful. A different, and perhaps more accurate way to look a knocking is to use our model to rpedct combustion chamber temperature. This can be done using the following formula (from Supercharged! Design, Testing and Installation of Supercharger Systems by Corky Bell): Combustion chamber temperature = (compression ratio)^0.28 x cylinder inlet temperature Where combustion chamber temperature is in ºF, compression ratio is the static compression ratio of the engine (eg “8” for a 8:1 engine), and cylinder inlet temperature is the temperature of the gases exiting the supercharger (in ºFabsolute). Guidance from Bell indicates that knocking will occur at an approximate combustion chamber temperature of 1075ºF. As an example, taking one of the data points for our non-water injection “small Norman” blown grey motor above, we see that the 7.25:1 engine at 110BHP would be running 8.8psi boost with a discharge temperature of 102ºC (676 ºFabsolute). Calculating through: Combustion chamber temperature = 7.25^0.28x676=1177ºF. This is over the guidance above of 1075ºC, indicating that knocking is likely. We can use the above formula to draw the graph below to use instead of the “rule of thumb” graph above: 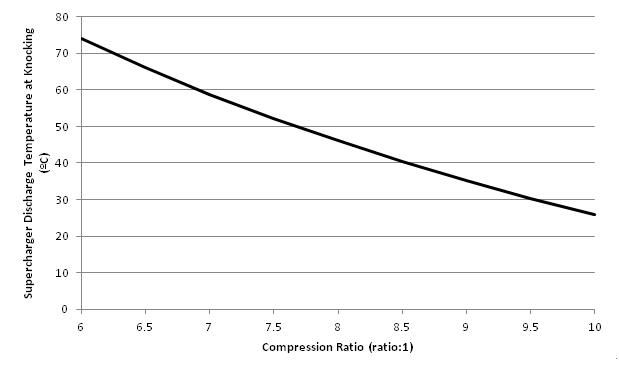 For our Holden grey motor (6.5:1 to 7.25:1, the graph shows us that we can expect knocking to occur somewhere between 55ºC and 65ºC, and for a red motor between 35ºC and 50ºC. This makes good sense when compared to the control implemented in Eldred’s 110 Deluxe water injector which kept the supercharger discharge temperature between 43º to 49ºC. So what can we do with the data above? If we take the limit for knocking to be 50ºC supercharger discharge temperature, and use our modelling from above, then we can see that without water injection our supercharged grey motor will perform like the following chart: 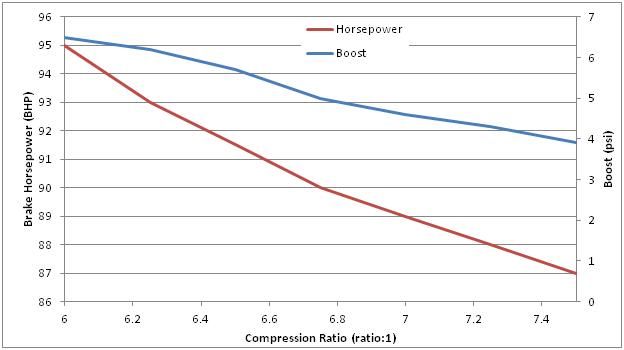 The chart shows that without water injection, our 7.25:1 (typical FB-EJ Holden) grey motor will be limited to about 88BHP at 4½psi boost, whilst an earlier FX-FJ grey motor at 6.5:1 is likely to be limited to around 91BHP at 5½psi. We can sneak a few more BHP out by decompressing the motor to 6:1 (by opening the heads or adding a decompression plate), but in reality we are pretty limited. In summary, the above modelling has thus delivered us two useful messages: • a supercharged grey engine can expect knocking to occur somewhere between 55ºC and 65ºC supercharger discharge temperature, with 50ºC a reasonable control limit, and • water injection is going to be a necessity on our blown grey unless we are happy with only 20% or so power increase. There are other ways of dealing with knocking (for example fuel and ignition) and I will cover these separately. Cheers, Harv (deputy apprentice Norman fiddler).
|
|
|
Logged
|
|
|
|
fcwrangler
|
 |
« Reply #34 on: October 02, 2013, 10:07:36 PM » |
0
|
Harv, A bit of info you may find interesting. Did a job at a performance centre today, they had a couple of VF Commodores having the new Magnuson supercharger kits fitted. One was a brand new GTS with 70 klms on the clock getting the full treatment. The guys said it would be good for around 550-600 rwkw. A real nice kit that makes the Norman look prehistoric. Jim
|
|
|
Logged
|
on the seventh day: God Made Holden
|
|
|
Harv
|
 |
« Reply #35 on: October 03, 2013, 06:58:06 AM » |
0
|
Cool - cheers Jim  . One of the tough bits with the Norman project is that peoples perception of supercharging has changed so much since the early 60's. With intercooling, EFI, electronic engine management and 10 points of extra octane at the pump, performance has really increased in leaps and bounds. Even the old Rootes blowers have made big steps with the twisted rotor concept developed by Eaton (then borrowed by Magnusson). When you look at a Norman running 5psi, no intercooling, carbed and mechanical engine management it can be a real challenge to say "OK... it will have more grunt, but not like a modern car". Like anything on a grey - going fast slowly  . Cheers, Harv
|
|
|
Logged
|
|
|
|
NES304
|
 |
« Reply #36 on: October 03, 2013, 09:59:33 AM » |
0
|
Harv, A bit of info you may find interesting. Did a job at a performance centre today, they had a couple of VF Commodores having the new Magnuson supercharger kits fitted. One was a brand new GTS with 70 klms on the clock getting the full treatment. The guys said it would be good for around 550-600 rwkw. A real nice kit that makes the Norman look prehistoric. Jim
Jesus Christ how much coin do people have?
|
|
|
Logged
|
|
|
|
Harv
|
 |
« Reply #37 on: October 03, 2013, 12:35:01 PM » |
0
|
Magnusson Heartbeat kit: $10,500 for 500kW. Norman supercharger: ~$5,000 for 90kW if you do the work yourself, $8,500 if you buy one from eBay. Not too sure a Magnusson will fit under an early Holden bonnet though  Cheers, Harv
|
|
|
Logged
|
|
|
|
FC427
nsw-club
Guru
   
Offline
Model: FC
Posts: 2457
I love YaBB 1G - SP1!
|
 |
« Reply #38 on: October 04, 2013, 07:25:25 AM » |
0
|
Harve you are yet to mention the Shoric blower [air craft cabin pressure] ??  that was also used by early drag racers ....And how good a blown Holden 6 looks and sounds ......FC427.......  [/URL]  [URL=http://s265.photobucket.com/user/FC427/media/IMG_3146.jpg.html]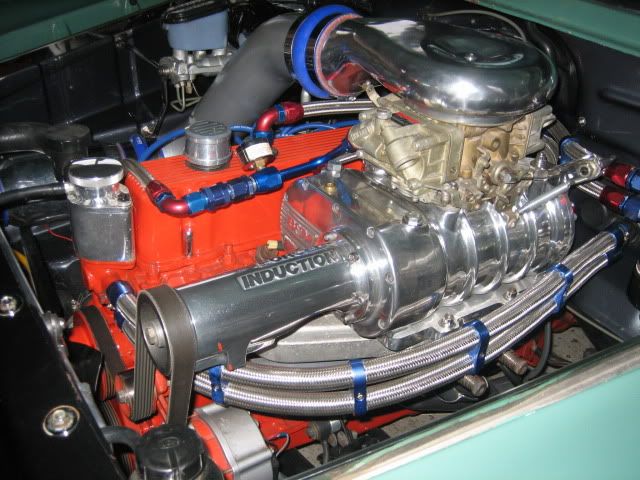 [/img]
|
|
|
Logged
|
As I lay rubber down the street I pray for traction I can keep, but if I spin and begin to slide please dear god protect my ride
|
|
|
Harv
|
 |
« Reply #39 on: October 04, 2013, 11:41:35 AM » |
0
|
No doubt about it, a blown red sounds cool. A blown grey is going to sound even cooler  . Havn't heard of Shoric superchargers before, and came up empt on a Google search. You're not thinking of Shorrock are you? I've got these in the diagram on my second post - they are eccentric vane units, very different to Norman (damn complex internally). A sketch of the internal configuration is shown in the 6th post. Cheers, Harv.
|
|
|
Logged
|
|
|
|
|